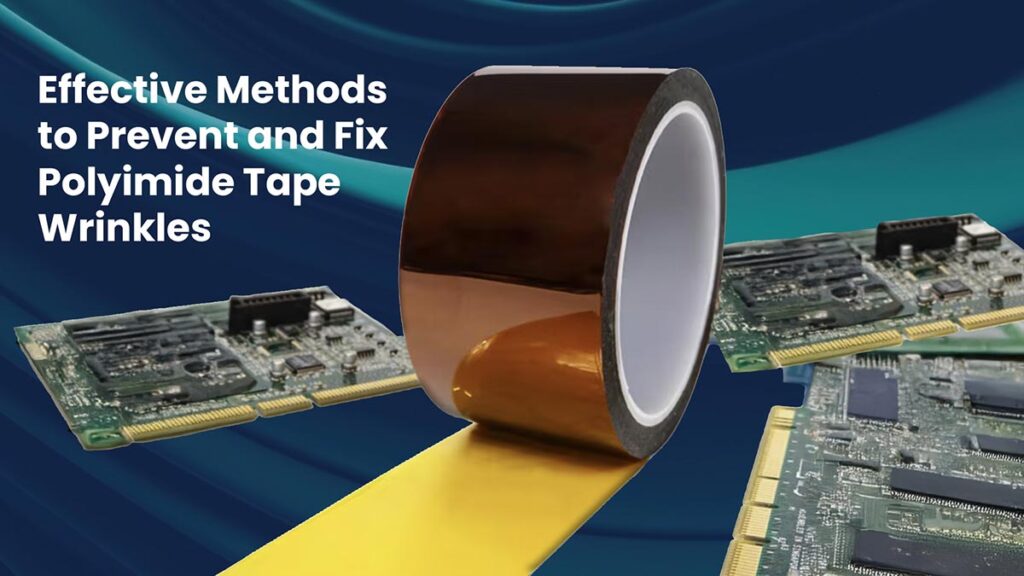
Polyimide Tape Tips for Smooth Application and Long-Term Performance
Polyimide tape plays a vital role in a variety of industrial applications, recognized for its durable and heat-resistant qualities. Whether utilized in aerospace, electronics, or motors and generators, polyimide tape offers solutions where high performance is required. However, achieving an optimal application can sometimes be a challenge. Wrinkles during application can compromise the effectiveness, leading to potential issues with performance and appearance. It’s essential to understand why these wrinkles occur and explore methods to prevent them, ensuring that the application remains smooth and efficient.
Imagine applying a sticker smoothly on a flat surface—any wrinkle or bubble can ruin the finish and its function. Just like that, polyimide tape needs careful handling to maintain its integrity. Working with polyimide tape can be tricky, but knowing the pitfalls and how to avoid them can be quite helpful.
Causes of Wrinkles in Polyimide Tape
Wrinkles in polyimide tape don’t just appear out of nowhere; they’re usually the result of a few common factors. Understanding these causes is the first step in avoiding them.
– Improper Application Techniques: Quite often, wrinkles arise from how the tape is applied. Without the right tension or speed, the tape can bunch up or misalign.
– Environmental Factors: The surrounding temperature and humidity can influence how the tape behaves, making a seemingly simple application more complex.
– Quality of the Tape: Not all tapes are created equal. Variations in manufacturing can lead to differences that affect how easily the tape can be applied without wrinkles.
Each cause can play a part in diminishing the tape’s performance. As these wrinkles affect how well the tape adheres and insulates, recognizing these factors early can ensure a smooth finish. The integrity of the application is crucial, and tackling these causes head-on helps maintain that integrity.
Prevention Techniques
Keeping polyimide tape free of wrinkles starts with good preparation and application methods. A few straightforward strategies can make all the difference in achieving a flawless finish.
1. Prepare the Surface: Before applying the tape, ensure the surface is clean and dry. Any dust, oil, or residue can create an uneven layer that promotes wrinkles.
2. Consistent Tension: Applying the tape with a uniform tension is key. Pulling too tightly or too loosely can cause it to stretch unevenly, leading to creases.
3. Temperature and Humidity: Control the environment where you’re applying the tape. Extreme temperatures might make the tape more pliable or brittle, while high humidity can affect adhesion.
4. Use the Right Tools: A roller or squeegee helps in smoothing out the tape during application. It ensures firm contact with the surface and minimizes air bubbles.
Focusing on these techniques helps to create a seamless application, preserving both the function and appearance of the tape.
Solutions for Wrinkled Polyimide Tape
Even with the best intentions, wrinkles sometimes happen. When they do, it’s important to know how to fix the situation before it hampers performance.
– Gently Lift and Reapply: If wrinkles appear during application, carefully lift the tape where appropriate and smooth it back down, ensuring even pressure across its surface.
– Use a Roller: For minor wrinkles, gently rolling over the surface might flatten them out without having to start over.
– Heat Application: In some cases, gently warming the tape with a hair dryer can make it more pliable, helping to smooth out the wrinkles. Be cautious with temperatures, keeping them within the tape’s safe range to avoid damage.
– Trim and Patch: For more significant wrinkles, cutting out the affected section and applying a patch may be the most effective approach.
Correctly addressing these wrinkles not only saves time but also guarantees that the tape’s performance remains intact.
Benefits of Proper Application
Applying polyimide tape correctly offers several advantages that enhance its performance across different industries. When wrinkles are absent, the tape can adhere more securely, providing consistent thermal and electrical insulation.
In environments like aircraft and aerospace, polyimide tape maintains equipment integrity at various temperatures. Meanwhile, in flexible printed circuitry, it allows components to function smoothly without interference or breaks caused by misapplied tape. Industrial sectors that rely on pressure-sensitive tapes benefit, too, with reduced downtime for checks and repairs when tape is reliably applied.
Proper application contributes to overall efficiency, saving time and resources while enhancing safety and functionality.
Wrapping Up Smoothly
Understanding how to prevent and address wrinkles in polyimide tape is essential for any field that uses this versatile material. From the factors leading to wrinkles to practical ways of addressing them, these insights help ensure a smooth and effective application every time. As you handle polyimide tape for your projects, these practical tips and solutions will aid you in maintaining its integrity and performance.
For industries seeking superior adhesive solutions, the right application of polyimide tape is key. Explore how APICAL® Polyimide Film enhances performance with polyimide tape to achieve seamless results in varied environments. Embrace improved efficiency and lasting reliability by discovering our specialized offerings today.